The Importance of DIN Thread Charts in Modern Manufacturing
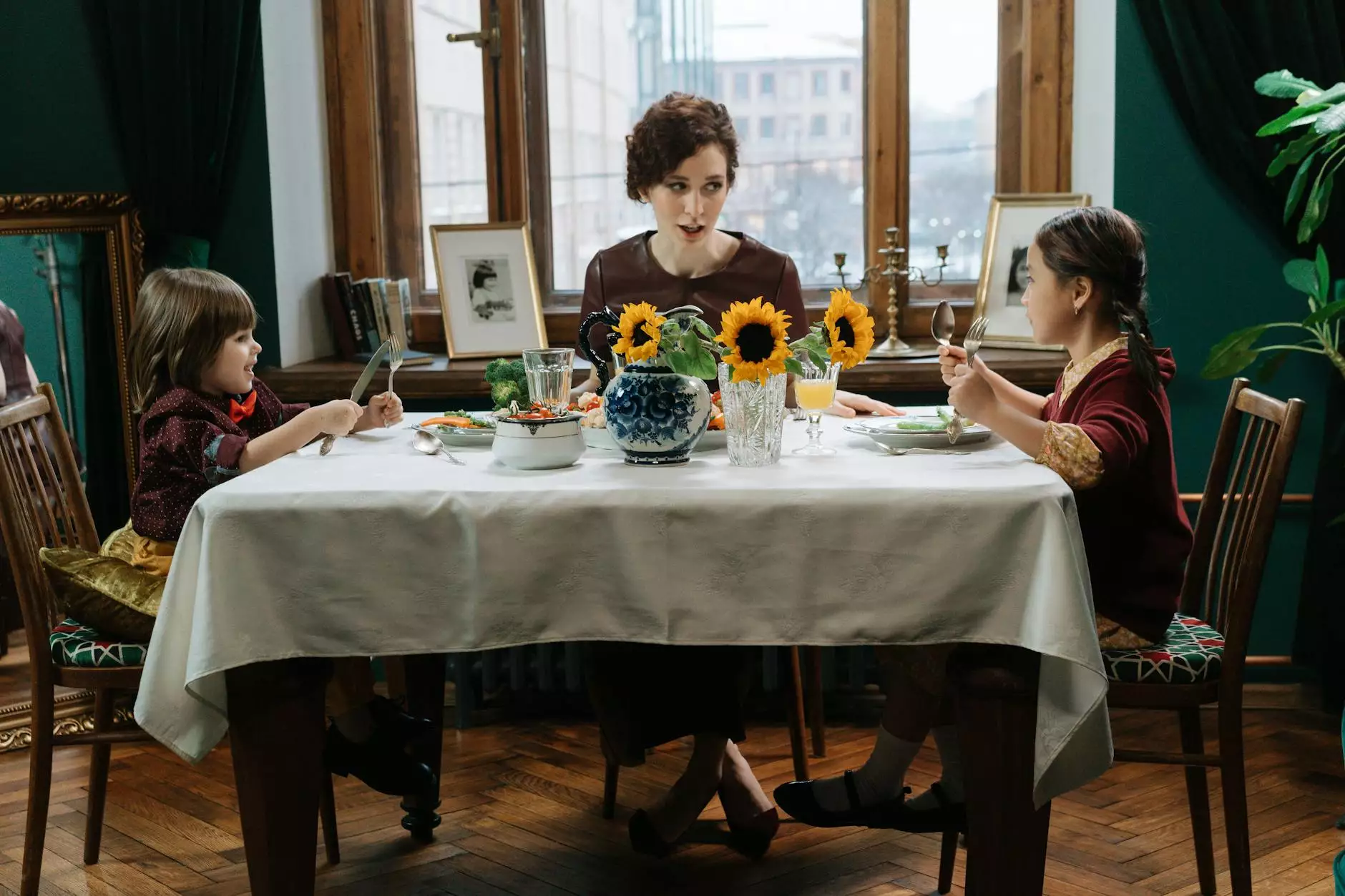
In the complex world of manufacturing, understanding precise specifications is critical to success. One such essential tool is the DIN thread chart. This article delves into what DIN threads are, their significance in manufacturing, and how they facilitate the production of quality fittings sold at fitsch.cn.
What are DIN Threads?
DIN stands for Deutsches Institut für Normung, which translates to the “German Institute for Standardization.” This institute is responsible for creating guidelines and standards across various industries, including engineering and manufacturing. DIN threads refer specifically to a set of standardized thread specifications developed for use in screws, bolts, and other fasteners.
The Role of DIN Thread Charts
A DIN thread chart is a comprehensive reference tool that details the specifications, dimensions, and tolerances for various DIN standardized threads. These charts are crucial for engineers and manufacturers as they provide precise measurements and guidelines to ensure that fasteners fit perfectly and function as intended.
Why Use DIN Thread Charts?
- Consistency: By adhering to established standards, manufacturers can ensure that products are consistent and interchangeable across different platforms.
- Quality Assurance: Utilizing DIN thread charts helps maintain a high level of quality in the manufacturing process, reducing the risk of defects.
- Efficient Design Processes: Engineers can streamline their design processes by referencing these charts, saving time and resources.
- Global Compatibility: As DIN standards are recognized worldwide, they help facilitate international trade and cooperation.
Understanding DIN Thread Designations
DIN thread designations are typically alphanumeric, indicating the specific traits of the thread. For example, a designation might include information such as the thread diameter, pitch, and tolerance class. Here is a breakdown of a typical DIN thread designation:
Components of DIN Thread Designation:
- Diameter: The nominal size of the thread.
- Pitch: The distance from one thread crest to the next.
- Tolerance Class: Indicates the allowable deviation in thread shape and size.
Applications of DIN Threads and Charts
DIN threads find applications in a wide range of industries, including automotive, aerospace, and construction. Let's explore some specific applications:
Automotive Industry
In the automotive sector, DIN threads are extensively used in vehicle assembly. From fastening engine parts to securing body panels, the reliability of screws and bolts based on DIN specifications is paramount for safety and performance.
Aerospace Sector
The aerospace industry demands the highest level of precision and reliability. Components must withstand extreme conditions, making the use of standardized threads essential. DIN thread charts aid engineers in selecting the right specifications for critical assemblies.
Construction
In construction, DIN threads are utilized in everything from structural supports to machinery. Ensuring that fittings and fasteners adhere to these standards protects infrastructure integrity.
Benefits of Using DIN Standardized Fittings
Implementing DIN standardized fittings has several advantages:
Enhanced Safety
Safety is a top priority in any manufactured product. DIN standards provide guidelines that are rigorously tested, ensuring that products are safe for use in critical applications.
Increased Efficiency
By using standardized threads, manufacturers can streamline their production processes. There is no need for custom solutions when off-the-shelf standardized parts will fit perfectly.
Cost-effectiveness
Standardization often leads to bulk production, which can lower costs. Using DIN fittings allows companies to purchase consistently sized components at competitive prices.
Challenges in Using DIN Threads
While the benefits of DIN standardized threads are numerous, there are challenges that manufacturers may face, including:
Complexity in Standards
The vast array of DIN standards can be overwhelming. It is crucial for manufacturers to stay updated on changes and ensure they are using the appropriate standards for their applications.
Sourcing Quality Components
Not all manufacturers supply parts that adhere to DIN standards. It is essential to source components from reputable suppliers to guarantee compliance with industry standards such as fitsch.cn.
The Future of DIN Threads in Manufacturing
As technology evolves, so too will thread standards. Innovations such as additive manufacturing (3D printing) and smarter manufacturing processes will drive adaptations in traditional DIN standards. Adaptability will become crucial as manufacturers seek to incorporate the latest technologies while adhering to safety and quality standards.
Conclusion
In conclusion, DIN thread charts are an invaluable resource in the manufacturing industry. They promote consistency, quality, and safety across sectors. As businesses like fitsch.cn continue to provide high-quality fittings, understanding and utilizing DIN standards will be essential for engineers and manufacturers alike. By leveraging these tools, the industry can ensure robust, reliable connections in various applications, paving the way for future advancements in manufacturing.
Explore More
For more information on fittings for sale and to ensure your projects adhere to international standards, visit fitsch.cn. Discover how quality and precision can enhance your operations and drive success in your industry.