Understanding Instrument Pipe Fitting: An In-Depth Exploration
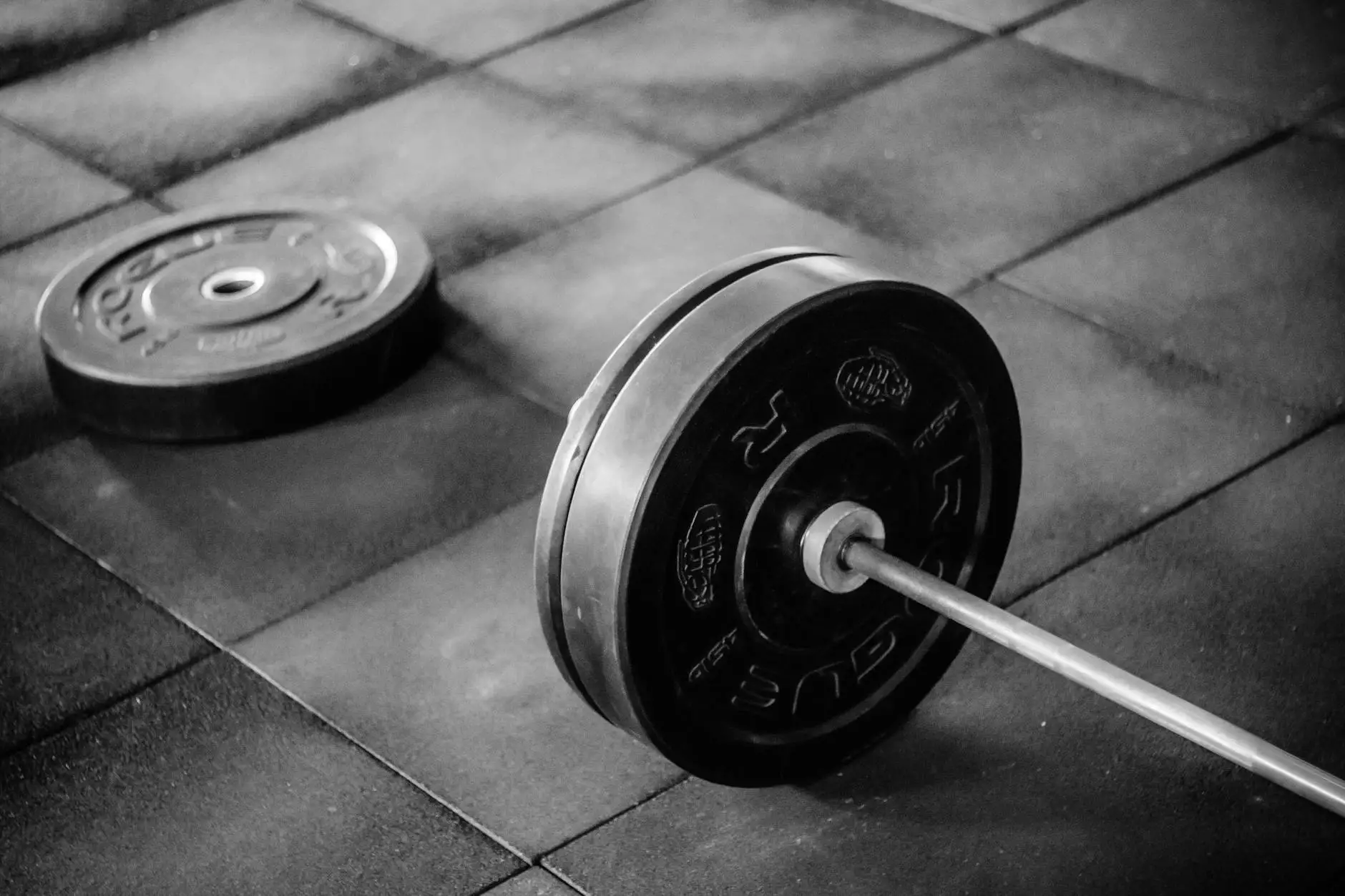
Instrument pipe fitting plays a critical role in various industries, including oil and gas, manufacturing, and process industries. These fittings ensure the integrity and efficiency of piping systems, which are essential for transporting fluids and gases safely and reliably.
What is Instrument Pipe Fitting?
Instrument pipe fitting refers to the specialized components that connect, direct, and regulate the flow of fluids and gases in piping systems. These fittings are designed to maintain the integrity and performance of the entire piping infrastructure, ensuring optimal operational standards.
The Importance of Instrument Pipe Fittings
The significance of instrument pipe fittings cannot be overstated. They are integral to:
- Ensuring Safety: Proper fittings reduce the risk of leaks and failures, which can lead to hazardous situations.
- Enhancing Efficiency: Correct fitting enhances the system's performance by minimizing pressure drop and preventing fluid turbulence.
- Long-Term Reliability: High-quality materials and precise engineering contribute to the durability and longevity of the fittings.
Types of Instrument Pipe Fittings
The market offers a wide variety of instrument pipe fittings, each tailored for specific applications. Here are some of the most commonly used types:
1. Elbows
Elbows are used to change the direction of the pipeline, typically at 90 or 45 degrees. They are crucial for navigating around obstacles and redirecting flow efficiently.
2. Tees
Tees are fittings that branch out from a main line. They are essential for creating multiple flow paths from a single source.
3. Couplings
Couplings connect two sections of piping together. They are vital for extending pipe runs and are available in various materials suited to different environments.
4. Reducers
Reducers are used to connect pipes of different diameters, allowing for a gradual transition between sizes, thereby maintaining flow efficiency.
5. Crosses
Cross fittings allow for four different flow paths and are used when a three-way connection is not adequate.
6. Caps and Plugs
Caps and plugs are used to terminate the end of a pipe or fitting, preventing the escape of fluids and maintaining system integrity.
Materials Used in Instrument Pipe Fittings
Choosing the right material for instrument pipe fittings is crucial for performance, durability, and compatibility with the transported substances. Common materials include:
- Stainless Steel: Known for its corrosion resistance and strength, making it suitable for a wide range of applications.
- Carbon Steel: Offers high strength and is often used in high-pressure applications; needs a protective coating to avoid rusting.
- Plastic: Lightweight and corrosion-resistant, ideal for less demanding applications.
- Brass: A preferred choice for plumbing fittings due to its excellent resistance to corrosion and good mechanical properties.
Applications of Instrument Pipe Fittings
Instrument pipe fittings are used across various sectors. Here are some key applications:
1. Oil and Gas Industry
These fittings are essential for transporting oil and gas safely through pipelines that can span hundreds of miles, requiring durable and reliable connection points.
2. Chemical Processing
In chemical plants, precise control of the flow of raw materials is critical. Instrumentation and fittings must withstand corrosive substances and high-pressure environments.
3. Water Treatment Facilities
Proper fittings help in effectively managing the flow and pressure of water through treatment systems, ensuring clean water supply.
4. HVAC Systems
Heating, Ventilation, and Air Conditioning (HVAC) systems rely on quality fittings to maintain airflow and proper climate control in buildings.
Benefits of Using Quality Instrument Pipe Fittings
Investing in high-quality instrument pipe fittings provides numerous advantages:
- Increased Safety: Reduces the likelihood of leaks and potential accidents.
- Cost-Effectiveness: Reliable fittings decrease the frequency of repairs and replacements, saving on maintenance costs.
- Improved Efficiency: Quality fittings contribute to optimal flow rates, leading to better overall system efficiency.
- Regulatory Compliance: High-quality fittings often meet stringent industry standards, ensuring compliance with regulations.
How to Choose the Right Instrument Pipe Fitting
Selecting the appropriate instrument pipe fitting involves several considerations:
1. Application Specifications
The first step is to identify the application requirements, including temperature, pressure, and the types of fluids being transported.
2. Material Compatibility
Ensure that the material of the fitting is compatible with the substances it will come in contact with to avoid corrosion and chemical reactions.
3. Size and Configuration
Proper sizing is essential for maintaining flow standards. Review the existing piping layout and choose fittings that match the dimensions required.
4. Quality Standards and Certifications
Look for fittings that meet international quality standards. Certifications guarantee that the products have undergone rigorous testing and meet regulatory requirements.
5. Supplier Reputation
Choose reliable suppliers, such as fitsch.cn, known for their expertise in providing high-quality instrument pipe fittings and excellent customer service.
Maintaining Instrument Pipe Fittings
Regular maintenance of instrument pipe fittings is essential for sustaining their functionality and longevity. Here are some maintenance tips:
- Regular Inspections: Schedule routine checks for wear, corrosion, and leaks. Early identification of issues can prevent major failures.
- Cleanliness: Ensure that the fittings remain free from debris or buildup that could impact flow and performance.
- Replacement of Damaged Fittings: Promptly replace any fittings that show signs of significant wear or damage to avoid system failures.
The Future of Instrument Pipe Fittings
The future of instrument pipe fittings looks promising, with advancements in technology and materials. Innovations such as:
- Smart Instrumentation: Integration of sensors that can monitor flow rates, pressure, and temperature in real-time.
- Advanced Materials: Development of new materials that offer better resistance to corrosion and extreme conditions.
- Sustainable Practices: Increasing focus on environmentally friendly materials and manufacturing processes.
Conclusion
In summary, instrument pipe fittings are fundamental components of piping systems across various industries. Their quality directly impacts safety, efficiency, and the overall performance of fluid and gas transportation. Businesses like fitsch.cn provide the essential fittings needed to ensure high standards in operation. Investing in quality fittings and maintaining them diligently will help in achieving long-term operational efficacy and safety.